Borrowing from HeraldNet.com comes the 500th Boeing 787 entering the
factory with its swagger. This 500th body is destine for Air France in the form
of a 787-9. Having this segway for a good 787 read while going forward without pause, is my humble space offered to do so.
Without further ado, here is the Herald Net offering for a reading assignment.
500th 787 at the back of the line depiction
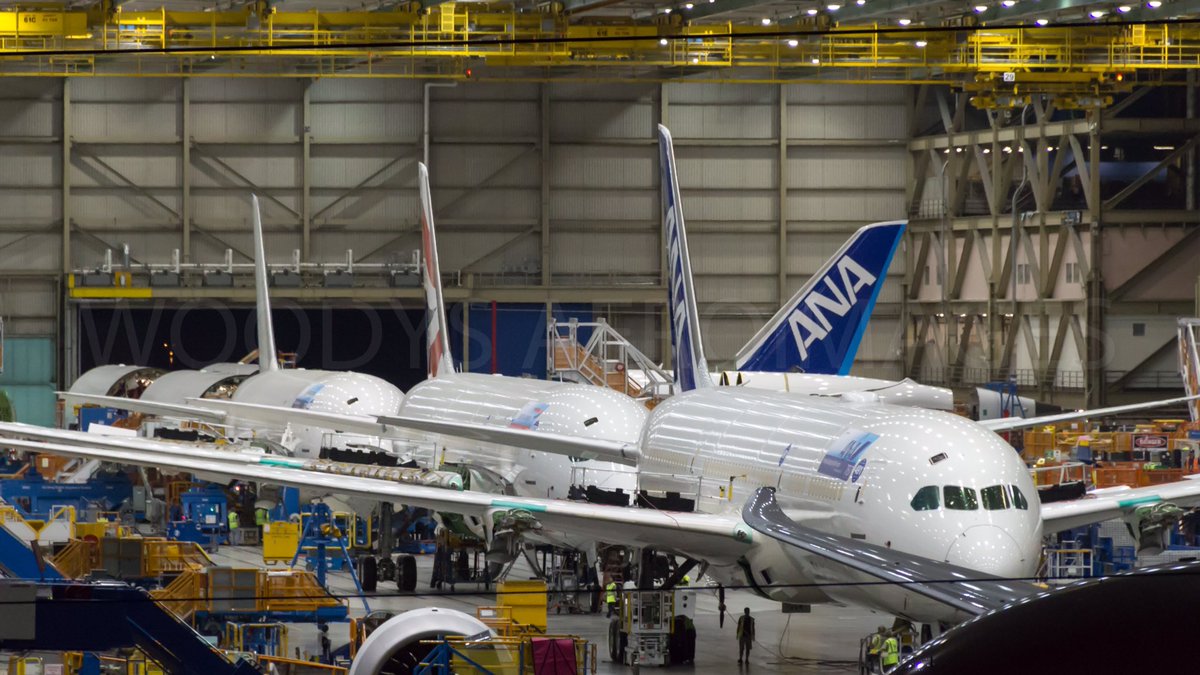
"...The airplane is in pieces, now, but it’s in the factory: the
500th Boeing 787.
Workers loaded the Air France 787-9 onto the Everett plant’s final
assembly line earlier this month, putting the program on track to be the
fastest to crank out 500 twin-aisle jetliners. Boeing’s plant here and in North
Charleston, South Carolina, are steadily delivering Dreamliners — nearly 12 a
month. And the 787s are making good on what matters most to airlines: the
company’s big claims to make an airplane that slashes operating costs and opens
new markets.
Boeing is working on further
upgrades to the jetliner’s cabin, which has already set new standards for
passenger comfort. No aerodynamic improvements are planned for now. However, Rolls-Royce’s
improved Trent 1000 TEN engine is expected to be online in
late 2017 — more than a
year late — offering operators even better
performance, said Bob Whittington, Boeing vice president and chief program
engineer for the 787.
After the plane’s
problem-plagued beginning, “the view is great” at 500, he said. It’s been five years today since Boeing delivered the first 787 to All
Nippon Airways of Japan. The delivery was more than three years late. But the
program’s early headaches — reliability
issues, production
backups, an emergency grounding due to smoking batteries, spiraling development
and production costs — are almost distant memories now. “We’re out of the dark
days,” he said. ‘Boeing magic’. The 787’s far-flung
supply chain relied heavily on outsourcing to cut development time and costs.
However, the aggressive strategy created logistical and financial migraines for
the Dreamliner program. Boeing committed huge resources to solving the issues,
including buying out its joint-venture partners in South Carolina. That opened
the door for the company to put a second final assembly line there in 2011.
Boeing matched its desire to
drastically reshape how modern jetliners come together with its ambition to
make the most advanced passenger plane. The 787 is the first jetliner with an
all-composite material body, whereas conventional airplane bodies rely on
aluminum alloys. The plane would be just as strong as an aluminum one, yet much
lighter. That, along with improved aerodynamics, more sophisticated software,
powerful new engines and other innovations, would make the plane much more
efficient than ones of similar size and range, Boeing promised.
But early 787s rolled out
overweight and customers were underwhelmed. Several airlines refused to take
delivery of the earliest Dreamliners, which started stacking up around Paine
Field.
Boeing poured money and people on the problems, and steadily worked through them.
“I call it the ‘Boeing Magic’ — how
people come together and take on problems and come up with solutions,” said
Michael Griego, a senior manager for the 787 supply chain. “It was amazing to
see” on the Dreamliner.
During those early days, Griego
spent long hours walking the production line with engineers and mechanics
addressing problem parts — what went wrong, where did it occur, and how best to
fix it now and stop it from happening again? “It was intense” work — and
important, too, she said.
“Those were good days.”
“When I remember the early days and how hard we struggled, I almost can’t believe where we are now,” Griego said. Almost there in 2012, Boeing delivered 46 787s, its first full production year. It delivered three times that many last year, and is on pace to do so again this year. The current production rate is 12 airplanes a month. Actual deliveries are slightly fewer.
The company plans to turn out 14
Dreamliners a month by the end of the decade, and the program is already
gearing up for the increase, although a Boeing exec said last month that there might
not be orders to support that pace.
“We’re not quite a turnkey
operation, but we’re almost there,” Griego said.
The company continues to smooth out
production. The 787’s use of automated machines required for making its
composite material airframe has flattened the production learning curve. That
helped the program rapidly increase production. But the cost of making an
airplane has not fallen at a similar pace.
That has many industry experts
skeptical about Boeing’s ability to get production so efficient that it can
make big enough profits off future deliveries to make up the nearly $28 billion
it has lost up to now. The company makes enough money from other programs and
services that it can absorb the 787 losses. The airplane maker keeps those
losses from bogging down its balance sheets through an accounting method called
deferred production cost. That has Boeing spread costs from today across the
hundreds of Dreamliners it plans to sell in years to come, while counting
future expected profits now. That approach helps buoy share price and,
proponents say, gives investors a more accurate view of the company over time.
Critics say it is using financial tricks to obscure reality.
Regardless, it also means Boeing
has less cash now to spend developing new, even shinier airplanes. Earlier this month, it closed one
787 stall on its flight line at Paine Field, where customers inspect the planes
and mechanics make last-minute fixes. At the height of the production problems,
dozens of 787s not ready for delivery were parked around the airport. Now, the
program has only eight dedicated flight line stalls. It closed a second
assembly line in Everett in 2015 as the South Carolina plant’s efficiency
improved.
In 2012, 16,800 people worked on
the 787 program in Washington, according to a state commissioned study.
The number is considerably less
now. Boeing does not publicly comment on how many people work on a specific
airplane program.
Put the coals to it in the factory,
“there are a lot of projects in the works for 2016 and 2017” to further improve
production and reduce costs, said John Barnfather, a senior manager for 787
manufacturing. He helps run the last spot on the assembly line in the factory.
“We put the coals to it right
here,” to finish any jobs that are behind schedule — something called “traveled
work” — before the plane moves outside, he said.
The amount of traveled work spiked
in 2014 after Boeing stepped up 787 production rate to 10 a month. It reached a
point that the company
stopped loading new planes onto the assembly line here for about two weeks in August of that year in order to catch up. The
flight line was crowded with factory crews and contractors tackling overdue
tasks. That amount is dramatically down these days, according to mechanics on
the program.
Boeing heavily tweaked the 787’s design, as the first 787-8s out of factory were too heavy to make good on the company’s performance promises. Early planes were dogged with part problems and other headaches for airlines. Then there were the smoking batteries, which led to all in-service 787s being temporarily grounded in early 2013, while Boeing and partners worked on a fix, which came a few weeks later.
“Planes always start heavy and get
lighter,” said Edmund Greenslet, an aviation industry analyst and publisher of Airline
Monitor. “Planes are
the opposite of people, who start light and get heavier.”
Engineers typically make design
improvements after a new plane starts performing in the real world. “You’re
looking to cut pounds wherever you can find them,” he said.
With more than 450 Dreamliners in
operation, the plane “is delivering so far on what was promised,” Greenslet
said.
The 787-9, which was first
delivered in mid-2014, is showing about 15 percent efficiency gains — measured
in fuel consumption per seat — over similar airplanes, such as 767-300ERs. The
smaller 787-8 is posting single-digit gains in fuel efficiency, he said.
The first 787-10, the
biggest Dreamliner, is slated to be delivered in 2018. It will be
assembled only in South Carolina.
Performance also is improving the more airlines fly the 787 and learn how to get the most out of the planes, he said.
Airlines have used the 787 to open more than
100 new routes between distant cities that would have been money-losers with older, less efficient jets.
For airlines, Dreamliners are now almost as dependable as 777s, the gold standard for dispatch reliability — a key metric in commercial aviation that tracks how often an airplane type leaves the airport gates within 15 minutes of schedule. The 777 is well above 99 percent. The 787 stumbled early on, but now is about 0.2 percentage points behind the 777, said Whittington, the 787’s chief engineer.
So far, in-service 787s have backed up Boeing’s promise to build a hardier, more problem-free plane. More than 30 Dreamliners have had their first major scheduled maintenance, called a C check. The findings are in line with the company’s expectations for wear and tear, he said.
During the checkup, mechanics scour
the airplane, pulling it apart to inspect major systems and components. A 767
is supposed to have a C check, which
can take nearly two weeks and cost about $700,000, every 18 months. It should have a
D check — the most intense inspection — every six years. Dreamliners can go
twice as long between inspections, saving airlines millions of dollars during a
plane’s lifespan.
So far, 787 is on track to realize
Boeing’s promise to cut maintenance costs by as much as 30 percent. “The amount
of unscheduled work at the C check point is dramatically less than for a 767 or
777,” he said.
“We took risks on technology, and
we took risks on a new supply base and production system. And we took risks on
schedule,” Whittington said. “And the airplane turned out to be great. The
risks we took on the airplane turned out to be all worth it.
“If I had something I would say do
differently, we might have not taken so many stretches on the supply base at
the same time that we were trying to compress our schedules,” he said. “It’s
just too much risk all at one time and taking too many giant leaps.”
To change aviation, “you have to
take bold steps,” and Boeing has proven its ability to deliver on bold steps
time and again, Whittington said. “It’s just built into our DNA.”...
Dan Catchpole: 425-339-3454; dcatchpole@heraldnet.com; Twitter:@dcatchpole.
No comments:
Post a Comment